Construction safety is critically important to protect workers, prevent accidents, and ensure compliance with legal and regulatory standards. A strong safety culture reduces injuries, minimizes project disruptions, and boosts productivity. By prioritizing safety through training, protective equipment, and hazard awareness, construction teams create a secure work environment that safeguards lives and supports successful project delivery.
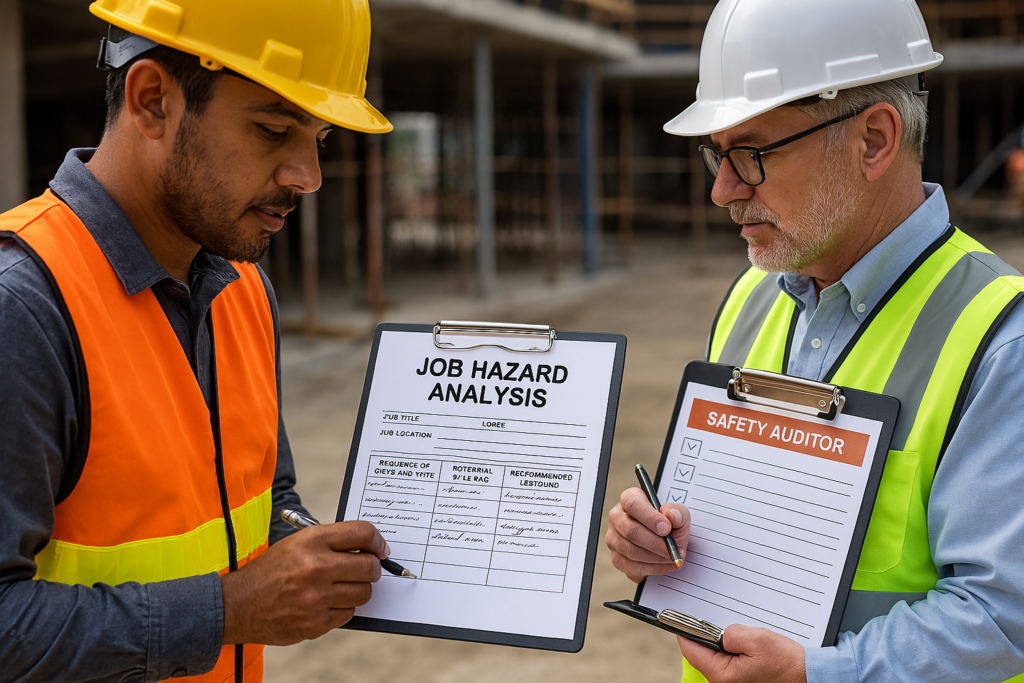
Safety FAQs
Why is construction safety management so important??
Construction is one of the most hazardous industries, and safety management is critical to protecting workers, the public, and project outcomes. A strong safety program reduces accidents, minimizes liability, and promotes a culture of accountability and care across the jobsite.
What does a Construction Safety Management Plan (CSMP) include?
A CSMP typically includes hazard identification, risk assessments, safety training, emergency response protocols, personal protective equipment (PPE) requirements, inspection schedules, incident reporting procedures, and corrective action tracking.
Who is responsible for safety on a construction site?
Everyone plays a role in jobsite safety, but primary responsibility lies with the general contractor, site supervisors, safety officers, and project leadership. Subcontractors, vendors, and field staff are also expected to follow and reinforce safety protocols.
What are the benefits of proactive safety management?
Proactive safety management reduces injuries, avoids costly delays, ensures compliance with OSHA and local regulations, and fosters team morale. It also enhances project quality by creating a stable, well-organized work environment.
How do you ensure compliance with safety standards?
We ensure compliance by developing site-specific safety plans, conducting regular audits and inspections, providing ongoing training, and maintaining open communication between the field, office, and client. Documentation and real-time reporting are central to our approach.
Can a strong safety program improve productivity?
Yes. Safe sites are efficient sites. When workers feel secure and organized, productivity increases, rework is minimized, and crews operate more confidently—leading to better outcomes and smoother project delivery.
Does your firm provide safety officers or audits?
Yes. We offer on-site safety professionals, third-party audits, job hazard analysis (JHA) support, and development of full Construction Safety Management Plans to help clients maintain a safe, compliant, and well-documented jobsite.
Substation Safety Awareness & Purpose of LOTO
Lockout/Tagout is a life-critical safety protocol used to ensure that dangerous energy sources are isolated and rendered inoperative before any maintenance or servicing work begins. In electrical construction, LOTO is essential to prevent unexpected energization, release of stored energy, or electrical arc incidents.
Key Steps in a LOTO Procedure
- Preparation for Shutdown
- Identify all energy sources (electric, hydraulic, pneumatic, etc.).
- Understand the system’s operation and energy flow diagrams.
- Notification
- Inform affected personnel that a shutdown and lockout will occur.
- Equipment Shutdown
- Shut down machinery or equipment using normal stopping procedures.
- Isolation of Energy Sources
- Physically disconnect energy using appropriate disconnecting means (e.g., circuit breakers, switches).
- Application of Lockout/Tagout Devices
- Apply locks and tags to each energy-isolating device by a qualified person.
- Tags must include the name, date, and reason for lockout.
- Release of Stored Energy
- Discharge capacitors, bleed off hydraulic/pneumatic lines, and block mechanical parts if necessary.
- Verification of Isolation
- Test the circuit with approved test equipment to verify zero-energy state before beginning work.
- Perform Work
- Proceed with maintenance or installation only after verification.
- Restoration of Energy
- Ensure tools and personnel are clear.
- Remove locks/tags only by the person who applied them.
- Restore power gradually with clear communication.
Common Violations
- Failure to de-energize before servicing
- Group LOTO mismanagement (multiple trades)
- Removal of someone else’s lock
- Inadequate verification/testing
- Incomplete identification of all energy sources
🔧 ELECTRICAL EQUIPMENT CLEARANCES
Clearance Philosophy
Electrical clearances refer to the minimum safe distances required between energized parts and personnel, or between energized components and grounded surfaces. These distances are dictated by equipment voltage ratings and environmental conditions.
Standards and Regulations
- NFPA 70E, NEC, and OSHA 1910 Subpart S / 1926 Subpart K establish the minimum approach distances.
- IEEE and utility-specific guidelines may apply in transmission/substation environments.
Examples of Minimum Working Clearances (NFPA 70E Table 130.4(D))
Voltage Range | Minimum Approach Distance (Unqualified) | Minimum Distance (Qualified) |
---|---|---|
50–300V | Avoid contact | As required with PPE |
301–750V | 3 feet 6 inches | As calculated per Arc Flash |
751–15kV | 10 feet | Approach only with clearance |
Note: Always refer to site-specific Electrical Safety Program and use the most restrictive standard applicable. – Owner may have their own Electrical Safety Program and Working Clearance Distances.
Clearance Roles and Responsibilities
- Switchman/Authorized Worker: Controls switching order and clearance documents
- Work Leader: Ensures proper grounding and safety barriers
- Safety Watch / Spotter: Prevents accidental encroachment during hot work
⚡ ARC FLASH BOUNDARIES & PPE
What is an Arc Flash?
An arc flash is a sudden release of energy due to an electrical fault — capable of generating temperatures over 35,000°F, intense pressure waves, flying shrapnel, and deadly burns.
Three Safety Boundaries Defined by NFPA 70E
- Arc Flash Boundary
- The distance from the source within which a person could receive a second-degree burn without proper PPE.
- Usually determined through incident energy analysis (e.g., 1.2 cal/cm²).
- Limited Approach Boundary
- For unqualified persons — distance where shock hazards exist; entry requires escort and PPE.
- Restricted Approach Boundary
- For qualified persons — requires PPE and written, approved energized work permit to cross.
PPE Categories for Arc Flash Protection (Based on Incident Energy)
PPE Category | Arc Rating (cal/cm²) | Typical Equipment |
---|---|---|
1 | 4 | Control panels ≤240V |
2 | 8 | 480V MCCs, panelboards |
3 | 25 | Large breakers, bus bars |
4 | 40+ | Switchgear, high-energy circuits |
Best Practices for Arc Flash Protection
- Perform arc flash hazard analysis and labeling for all energized equipment.
- De-energize whenever possible.
- Use properly rated PPE: suit, gloves, face shield, balaclava, boots.
- Verify equipment ratings and boundaries before beginning work.
- Use insulated tools and test-before-touch protocol.
🔐 INTEGRATING LOTO, CLEARANCE, & ARC FLASH INTO CONSTRUCTION SAFETY PROGRAMS
What BGA Engineering Promotes
- Zero-Energy Work Culture: All work should be planned de-energized unless otherwise justified.
- Standardized Clearance and Switching Procedures: Align with utility standards and OSHA lockout protocols.
- Site-Specific Energized Work Permitting: For rare cases when live work is justified.
- Training and Qualification: All electrical workers must be NFPA 70E and OSHA 1910.269 trained.
- PMIS Integration: Digital permits, lockout logs, PPE inspection logs, and boundary drawings tracked in platforms like Procore or Primavera.
Field Hazards & Mitigation Strategies
Hazard | Mitigation |
---|---|
Unexpected energization | Rigid LOTO policy with visual lock indicators and LOTO audit trails |
Arc flash burns | Pre-job planning, rated PPE, calculated boundaries |
Working in confined switchgear rooms | Ventilation, buddy system, restricted entry protocols |
Coordination with other trades | Group lockout procedures and daily safety briefings |
✅ FINAL THOUGHT
LOTO, electrical clearances, and arc flash protection aren’t just checkboxes on a safety form — they’re core to life preservation on electrical construction sites. An informed, disciplined crew following proper protocols can prevent irreversible injuries and ensure project success without compromise.